Environmental
Health and Safety
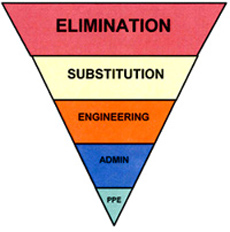
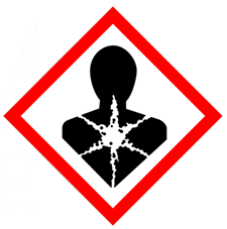
General
Safety Training
Revised
February 23, 2018
Outline
- Purpose
- Chancellor's Policy Statement
- Safety Responsibilities
- General Safety Rules
- Hazard Communication
- Reducing Hazard Exposure
- Fires and Fire Extinguishers
- Safety Support
Purpose
This training provides general safety guidance
for LSUHSC faculty, staff and students. It is the first of four quarterly safety
presentations issued via the Knowledge Delivery System as required by the State
Office of Risk Management.
These quarterly safety presentations provide
information generally applicable to all personnel. It is the responsibility of
all supervisors to augment this training with site-specific safety training
required in their work areas. For instance, while this presentation provides
general guidance on Hazard Communication, personnel who work with hazardous
chemicals must receive training on the hazards associated with those particular
chemicals.
Chancellor's
Policy Statement
The LSU Health Sciences Center New Orleans is
committed to providing a safe and healthy environment for all faculty, staff,
students and visitors; and conducting its mission in compliance with all
applicable environmental health and safety laws and regulations.
As Chancellor, I am responsible for ensuring
that the Health Sciences Center operates safely to minimize health hazards,
reduce the risk of injury, and maintain environmental compliance. Senior
leadership and all supervisors share in this responsibility with me, and will
ensure that all activities under their control are performed safely and in
accordance with current policies and guidelines. A primary role of the
Environmental Health and Safety (EH&S) Department is to oversee the safety
and environmental programs, and provide consultative services; contact EH&S
if you require assistance for any aspect of your safety and environmental
programs.
Maintaining a safe and healthy environment
requires the involvement of all faculty, staff and students. All members of the
Health Sciences Center community are responsible for their own safety and shall
set a personal example of safe practices for other members of the community.
Your commitment to safety and environmental compliance plays a critical role in
support of the Health Sciences Center's mission to provide world-class
education, research and public service.
Safety
Responsibilities
Vice Chancellors, Deans, Directors, and
Department Heads shall implement the safety program in their areas of
administrative responsibility and are responsible for the safety of the
personnel under their supervision. They will ensure that these personnel are:
- Familiar with safe work practices.
- Informed of hazards in their work area.
- Provided with the proper training and supervision in
order to perform their work safely.
Supervisors, Foremen, and Managers are also
responsible for the safety of the personnel under their supervision and will:
- Train employees in the safe use of equipment and in
safe work practices specific to the workplace.
- Correct any unsafe acts and unsafe conditions.
- Report and investigate accidents.
- Inspect their work areas for compliance with safe work
practices and to identify potential hazards.
- Ensure new employees and employees who are assigned new
tasks are trained on safety procedures before starting work.
Individual personnel are responsible for their
personal safety and will:
- Follow prescribed safety rules and regulations.
- Immediately report safety hazards to their supervisor.
- Report to the supervisor all incidents/accidents,
including "near misses", and any change in health status if it
may be due to a job-related activity.
- Seek guidance from their supervisor if there is any
uncertainty on any issue that may impact workplace safety.
The Environmental Health and Safety Department
is the principal provider and coordinator of all LSUHSC safety requirements, to
include:
- Providing resources to assist with the identification,
evaluation, and control of hazardous situations.
- Providing assessments for research laboratories and
shops working with potentially hazardous chemicals, biological or physical
agents or processes.
- Providing general safety training, hazardous waste disposal,
and occupational safety and health exposure evaluations.
- Developing and issuing rules and procedures.
General
Safety Rules
Adherence to the following safety rules reduces
the risk of mishaps:
- Don't smoke or use tobacco products on campus.
- Don't engage in horseplay.
- Before beginning work, notify your supervisor of any
permanent or temporary impairment that may reduce your ability to perform
in a safe manner.
- Use personal protective equipment (PPE) to protect
yourself from potential hazards that can't be eliminated.
- Operate equipment only if you are trained and
authorized.
- Inspect your workstation for potential hazards and
ensure that equipment/vehicles are in safe operating condition before use.
- Immediately report accidents, near misses, and property
damage to your supervisor regardless of severity.
- Immediately report any potentially unsafe condition or
act to your supervisor.
- If there is any doubt about the safe work method to be
used, consult your supervisor before beginning work.
- Follow recommended work procedures outlined for the
job, including safe work practices outlined in the job safety analysis,
standard operating procedure, or owner's manual.
- Maintain an orderly environment and work procedure.
Store all tools and equipment in a designated place. Place scrap and waste
material in a designated container.
- Fasten restraint belts. Do not use cell phones while
operating a government vehicle or while using your personal vehicle or
rental car for official business.
Hazard
Communication
- You have a right to know of the hazards in your
workplace and must be provided with the training and equipment necessary
to protect you from these hazards.
- A substance is "hazardous" if classified as
either a "physical hazard" (e.g., flammables, explosives) or a
"health hazard" (e.g., carcinogen, hepatotoxic, mutagen).
- Each laboratory or shop that uses hazardous materials
shall have a plan that addresses: proper handling, storage and disposal of
the hazardous materials; maintenance of Safety Data Sheets; use of
Personal Protective Equipment (PPE) and other safety equipment (e.g., fume
hoods); and site-specific training that is documented in writing.
- The site-specific training is required:
- Within 30 days of
employment;
- When working in a new
area;
- Whenever a new material
or procedure is introduced into the workplace;
- Whenever the Department
Head or Supervisor determines that refresher training is in order or
- At least annually.
- OSHA has implemented the Globally Harmonized System
(GHS) of Hazard Classification and Labeling of Chemicals.
- GHS makes two primary changes to the prior program:
- Material Safety Data
Sheets (MSDS) have been replaced by Safety Data Sheets (SDS).
- New labeling and
pictograms.
Safety
Data Sheets
- The previous chemical safety programs employed Material
Safety Data Sheets, which are written in a variety of formats.
- GHS changed the name to Safety Data Sheets, and standardized
the sections and information contained in the document.
Safety
Data Sheets
The new SDS format has 16 standardized sections:
- Identification
- Hazard(s) identification
- Composition of
ingredients
- First-aid measures
- Fire-fighting measures
- Accidental release
measures
- Handling and storage
- Exposure control/PPE
- Physical and chemical
properties
- Stability and reactivity
- Toxicological
information
- Ecological information
- Disposal considerations
- Transport information
- Regulatory information
- Other information
SDS-Example
of the New Format
GHS
Labels
- Similarly, the previous chemical labeling systems have
non-standardized labels that look different for the same product. Labels
also differ from country to country.
- Required GHS Product Label Elements:
- Product identifier and
chemical name.
- Signal words - use
"Danger" or "Warning" to indicate risk level.
- Pictograms.
- Hazard statements.
- Precautionary information.
- Supplier identifier.
- Although the label formatting is not standardized, all
labels will contain the six items listed above.
Example
Label
(Click or tap image for expanded view)
Pictograms
- The old hazard symbols,
called "pictograms" were also different from country to country.
GHS updates these to a standardized system for hazard communication.
- GHS uses nine
pictograms, which contain a black picture, indicating a hazard, set inside
a red diamond. The pictograms are shown below:
New
Pictograms
(Click or tap image for expanded view)
Transport
Pictograms
When chemicals are being transported a different
set of pictograms are used on the packaging.
- The Department of Transportation had already adopted
the GHS transport pictograms, so nothing will change. Transport pictograms
are shown below for reference.
- Where a transport pictogram appears, the GHS pictogram
for the same hazard should not appear. Transport pictograms will occur on
the outside of the box the chemical is packaged in.
(Click or tap image for expanded view)
Reducing
Hazard Exposure
The first consideration for controlling hazards
is to eliminate the hazard or substitute a
less hazardous material or process. When it is not possible to eliminate a
hazard, you should control the hazard using the following methods (in order):
- Engineering.
- Administrative.
- Personal Protective Equipment (PPE).
Applying this hierarchy is a systematic approach
to identify the most effective method of risk reduction. The highest-level
feasible control should be selected.
Engineering
Controls
- Engineering controls
minimize employee exposures by either reducing or removing the hazard at
the source or isolating the worker from the hazards.
- Examples of common
engineering controls used at LSUHSC include chemical fume hoods,
biological safety cabinets, and machine guards for power tools.
- Ensure all equipment
requiring inspection and testing is currently certified.
- Maintain and follow the
manufacturer's operating instructions for all engineering control
equipment.
- Users of engineering
control equipment must be familiar with their purpose, capabilities and
limitations prior to use.
Administrative
Controls
Administrative controls significantly limit
daily exposure to hazards through policies and procedures that provide guidance
for safe work practices and standard for behavior.
Examples include Job Safety Analyses (JSA) (see EH&S -400.04, Job Safety Analysis
Policy for performance guidance), standard operating procedures
(SOP), job rotation, training, signs and warning labels, personal hygiene,
housekeeping and maintenance.
Administrative controls do not remove hazards,
but help to limit or prevent exposure to the hazards.
Personal
Protective Equipment
- Personal Protective Equipment (PPE) is a device or
clothing worn by a worker to help prevent direct exposure to hazards.
- PPE is the least preferred method of protection, and
should be used following implementation of engineering and administrative
controls methods.
- Examples include respirators, hearing protection,
gloves, lab coats and safety glasses.
- Proper selection of PPE is crucial since one type of
PPE will not work with all types of hazards. Contact Environmental Health
and Safety for assistance with PPE selection.
Fires
- If you see a fire or
smoke, PULL the closest fire alarm pull station.
- ALERT others of the
pending emergency and begin a calm and immediate evacuation of the
building. Close the door(s) to your office or classroom to confine the
fire.
- CALL University Police
(568-8999) or 911 and provide:
- Your name and the
telephone number.
- The exact location of
fire or smoke.
- The type of fire
(electrical, flammable liquid, trash, etc.).
- The extent of the fire
(severity and/or amount of smoke).
Fire
Extinguishers
- All buildings are
equipped with automatic fire sprinkler systems. These systems activate
when heat melts a sensing element in the sprinkler head.
- All buildings are also
equipped with fire extinguishers, primarily type ABC extinguishers, which
are effective against wood, paper and plastics; flammable liquids; and
electrical fires.
- If you choose to use a
fire extinguisher, ensure you follow the guidelines below.
Fire
Extinguisher Guidelines
Never
fight a fire:
- If the fire is larger than the volume of a typical
trash can.
- If you must fight the fire with your back to an escape
exit.
- If the fire can block your only escape.
How
to operate a fire extinguisher:
- Use the PASS method. (Pull, Aim, Squeeze and Sweep)
Miscellaneous
Fire Guidelines
All open flames, open burns and the use of
pyrotechnics/fireworks, both indoors and outdoors, are strictly
prohibited at the Health Sciences Center except for:
- Classroom or laboratory:
Bunsen burners may be used in the course when conducted under the supervision
of the instructor.
- Hot Work Permit Program:
Open flames are permitted when covered by the Hot Work Permit Program.
Safety
Support
- If you need assistance
performing a hazard assessment for your shop or lab, or if you identify a
safety issue you can't correct yourself, contact Environmental Health and
Safety at 568-6585 or safety@lsuhsc.edu.
- LSUHSC has four
committees (General, Biological, Chemical and Radiation Safety) comprised
of faculty and staff that address safety concerns. If you have an issue of
concern that you would like to have a committee address, contact
Environmental Health and Safety.